An In-depth Overview of Container Welding Evaluation Requirements and Methodologies for Improved Weld High Quality and Efficiency
The importance of welding inspection standards in the manufacturing of containers can not be overstated, as they work as the foundation for making certain weld integrity and operational dependability. Numerous examination techniques, including aesthetic analyses and advanced non-destructive testing approaches, are crucial in determining prospective problems that can endanger efficiency. Sticking to governing criteria not just improves weld high quality however likewise alleviates the danger of expensive failures. As we explore the nuances of these approaches, it becomes crucial to think about exactly how a methodical method can transform current techniques and bring about considerable enhancements in results.
Relevance of Welding Evaluation Requirements
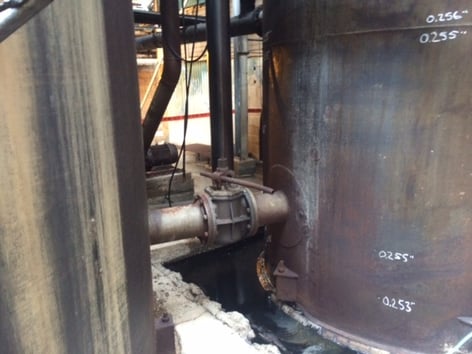
Welding examination standards include a series of standards, consisting of product specifications, welding procedures, and qualifications of workers included in the welding procedure. By applying these standards, organizations can systematically determine and correct prospective flaws, consequently lowering the chance of pricey repairs or catastrophic failures. Extensive assessment practices foster a society of liability and accuracy, encouraging welders to maintain high degrees of workmanship.
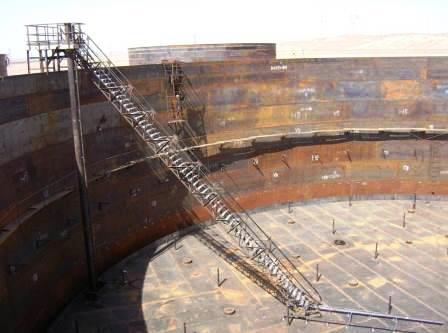
Common Welding Examination Techniques
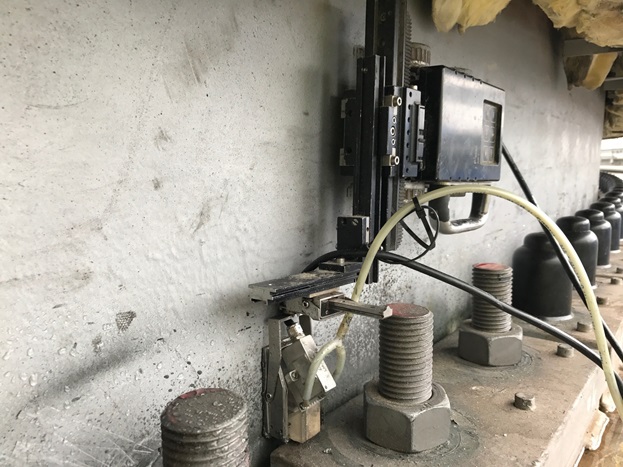

Ultrasonic Checking (UT) is an additional prevalent method, utilizing high-frequency acoustic waves to discover inner defects that might not show up externally. This method is especially reliable for identifying gaps or inclusions within the weld steel. Magnetic Fragment Evaluating (MT) is likewise commonly utilized, particularly for ferromagnetic products, as it reveals surface area and near-surface issues via the application of magnetic areas and ferrous particles.
Additionally, Liquid Penetrant Screening (PT) spots surface-breaking problems by applying a penetrant to the weld and after that using a programmer to extract the penetrant. Each of these techniques adds to a thorough evaluation method, ensuring that welds meet the rigid top quality standards needed in storage tank building.
Regulatory Standards and Conformity
Regulative requirements and compliance are crucial parts in ensuring the safety and security and integrity of welded structures in container building - Tank Welding Inspection. These standards offer to establish minimum requirements for material residential or commercial properties, welding procedures, and evaluation methods, consequently minimizing the threat of architectural failings and improving general performance
Trick organizations, such as the American Culture of Mechanical Engineers (ASME) and the American Welding Culture (AWS), give standards that are commonly embraced in the sector. Compliance with these standards not only ensures adherence to ideal techniques however also satisfies lawful and contractual commitments, securing the rate of interests of stakeholders.
Regulative bodies frequently mandate adherence to specific codes, such as ASME Code Section IX for welding credentials and API 650 for bonded storage tanks. These codes describe needs for welding techniques, certifications of personnel, and testing approaches to verify weld stability.
Regular audits and examinations are important to preserving compliance, as they help identify deviations from developed criteria. Non-compliance can result in substantial penalties, project hold-ups, and security hazards. Therefore, a durable understanding of regulative standards and a commitment to compliance are vital in accomplishing top quality and long lasting welded container frameworks.
Non-Destructive Testing Methods
Exactly how can the stability of bonded frameworks be guaranteed without causing damages? Non-destructive screening (NDT) methods provide a robust service, allowing examiners to examine weld top quality without endangering the product - Tank Welding Inspection. Amongst one of the most usual NDT strategies are ultrasonic screening (UT), radiographic screening (RT), magnetic fragment screening (MT), and color penetrant screening (PT)
Ultrasonic screening utilizes high-frequency sound waves to identify internal problems and characterize product residential properties. It offers specific dimensions and is specifically efficient for thick materials. Radiographic testing involves passing X-rays or gamma rays via the weld, developing pictures that expose architectural problems such as cracks or voids. This method is very useful for analyzing the integrity of complex welds.
Magnetic particle screening is fit for ferromagnetic materials, where magnetic areas disclose surface his comment is here area and near-surface discontinuities. Dye penetrant testing uses a fluid color to highlight surface-breaking defects, making it a reliable method for non-porous materials.
Each of these NDT methods has unique advantages, enabling extensive analyses tailored to specific materials and welding procedures. By executing these strategies, sectors can guarantee the dependability and security of welded structures, inevitably boosting general performance.
Enhancing Weld Quality Through Inspection
Reliable assessment plays a vital role in enhancing weld top quality, acting as an important checkpoint in the manufacture procedure. By identifying prospective issues early, evaluations alleviate the threat of endangered structural integrity and ensure compliance with market criteria. Using a mix of aesthetic examinations, non-destructive testing (NDT) methods, and mechanical analyses, examiners can spot concerns such as porosity, fractures, and insufficient blend.
Applying a durable examination method not just boosts the general top quality of welds however likewise promotes a society of accountability among welders and producers. Normal training and accreditation of assessment personnel guarantee that they are furnished with the needed skills to acknowledge and address possible troubles properly. This aggressive technique lessens rework and connected costs, ultimately contributing to project performance.
In addition, detailed documents of evaluation go to these guys searchings for gives important understandings into reoccuring problems, promoting continual enhancement in welding practices. By leveraging advanced modern technologies, such as automated ultrasonic screening or digital radiography, weld top quality can be enhanced with much more precise examinations. In final thought, an extensive inspection procedure is indispensable in accomplishing top quality welds, ensuring security, reliability, and long life in storage tank fabrication.
Conclusion
In final thought, the implementation of extensive tank welding examination criteria and methodologies is essential for ensuring weld integrity and performance. By utilizing a mix of visual evaluations, non-destructive testing methods, and adherence to regulative criteria, organizations more helpful hints can efficiently determine and reduce prospective problems. Fostering a society of accountability amongst welders better enhances the high quality of welding procedures. Ultimately, these methods add to reduced architectural failings, reduced repair work costs, and boosted functional effectiveness within the industry.
Comments on “The Relevance of Expert Tank Welding Inspection Solutions”